Automatisierte visuelle Inspektion
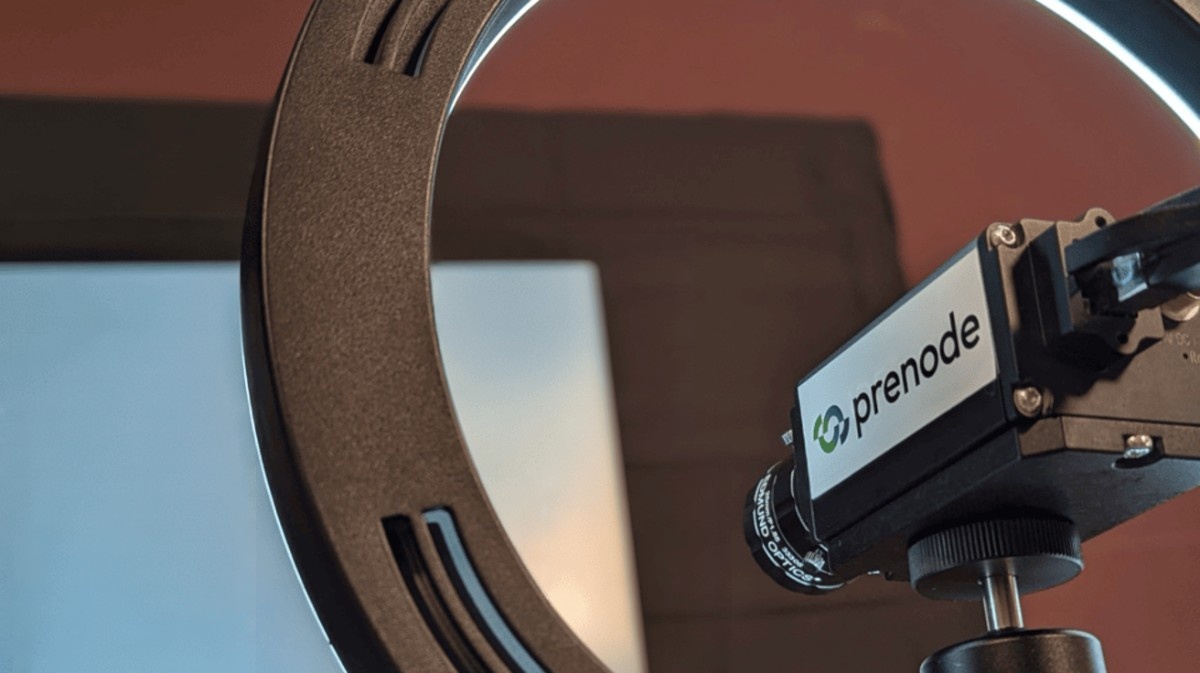
Die visuelle Inspektion ist ein essenzieller Bestandteil der Qualitätssicherung in der industriellen Produktion. Sie dient dazu, fehlerhafte Produkte zu identifizieren, bevor sie den Endkunden erreichen. Während die manuelle visuelle Inspektion über Jahrzehnte hinweg der Standard war, bringen moderne Technologien auf Basis von Künstlicher Intelligenz und Bildverarbeitung entscheidende Verbesserungen. In diesem Artikel beleuchten wir die Herausforderungen der manuellen Inspektion, die Vorteile der automatisierten Prüfung und den technischen Aufbau solcher Systeme.
Probleme bei der manuellen visuellen Inspektion
Die manuelle visuelle Inspektion ist in vielen Fertigungsbetrieben noch weit verbreitet, bringt jedoch eine Vielzahl an Herausforderungen mit sich. Einer der größten Nachteile liegt in der inkonsistenten Beurteilung von Fehlern. Menschliche Kontrolle ist naturgemäß subjektiv – Faktoren wie Tagesform, Konzentration oder Erfahrung des Prüfers beeinflussen die Qualität der Bewertung. Das führt dazu, dass Fehler unterschiedlich erkannt oder sogar übersehen werden.
Hinzu kommt, dass manuelle Prüfprozesse meist nur stichprobenartig erfolgen. Diese begrenzte Prüftiefe birgt das Risiko, dass fehlerhafte Teile unentdeckt bleiben und weiterverarbeitet oder ausgeliefert werden. Gleichzeitig sind visuelle Kontrollen zeitaufwendig. Lange Prüfzeiten verlangsamen den Produktionsprozess, erzeugen Engpässe und verringern die Effizienz – besonders bei steigenden Stückzahlen oder hoher Produktvielfalt.
Auch wirtschaftlich ist die manuelle Inspektion problematisch. Die Kosten für qualifiziertes Prüfpersonal sind hoch, und zusätzliche Aufwendungen entstehen durch Ausschuss, Nacharbeit und ineffiziente Abläufe. All das wirkt sich negativ auf die Profitabilität aus. Werden Qualitätsmängel nicht rechtzeitig erkannt, kann das zudem zu Reklamationen und unzufriedenen Kunden führen. Das Vertrauen in die Marke leidet – und damit auch die langfristige Kundenbindung.
Ein weiteres Problem liegt in der fehlenden Standardisierung. Da Prüfprozesse stark von einzelnen Personen abhängen, sind die Ergebnisse schwer vergleichbar und kaum reproduzierbar. Das erschwert sowohl die Qualitätskontrolle als auch die kontinuierliche Optimierung der Prozesse.
In Summe zeigt sich: Die manuelle visuelle Inspektion ist anfällig, kostenintensiv und zunehmend ein limitierender Faktor für produzierende Unternehmen.
Vorteile durch automatisierte visuelle Inspektion
Moderne, KI-gestützte Inspektionssysteme erkennen selbst kleinste Mängel, die dem menschlichen Auge entgehen. Sie arbeiten mit hoher Konsistenz und liefern reproduzierbare Ergebnisse, unabhängig von äußeren Einflüssen wie Ermüdung oder subjektiven Einschätzungen.
Automatisierte visuelle Inspektion kann direkt in die Produktionslinie integriert werden. Dadurch werden alle produzierten Teile geprüft, nicht nur Stichproben. Dies minimiert das Risiko, fehlerhafte Produkte auszuliefern, und ermöglicht eine sofortige Reaktion auf Qualitätsprobleme.
Die Reduktion von Ausschuss und Nachbesserungen spart Unternehmen erhebliche Kosten. Darüber hinaus liefern Inspektionssysteme wertvolle Analysedaten, mit denen Produktionsprozesse weiter optimiert werden können. Langfristig führt dies zu einer verbesserten Effizienz und Produktqualität.
KI-basierte Inspektionssysteme können schnell für neue Produktvarianten trainiert werden, was eine flexible Anpassung an unterschiedliche Anforderungen ermöglicht. Zudem lassen sich diese Systeme problemlos auf mehrere Produktionslinien oder Standorte erweitern.
Alle erfassten Inspektionsdaten können gespeichert und analysiert werden. Dadurch lassen sich langfristige Qualitätsprobleme identifizieren und gezielte Maßnahmen zur Fehlervermeidung ergreifen. Unternehmen erhalten so wertvolle Einblicke in ihre Produktionsprozesse und können diese kontinuierlich verbessern.
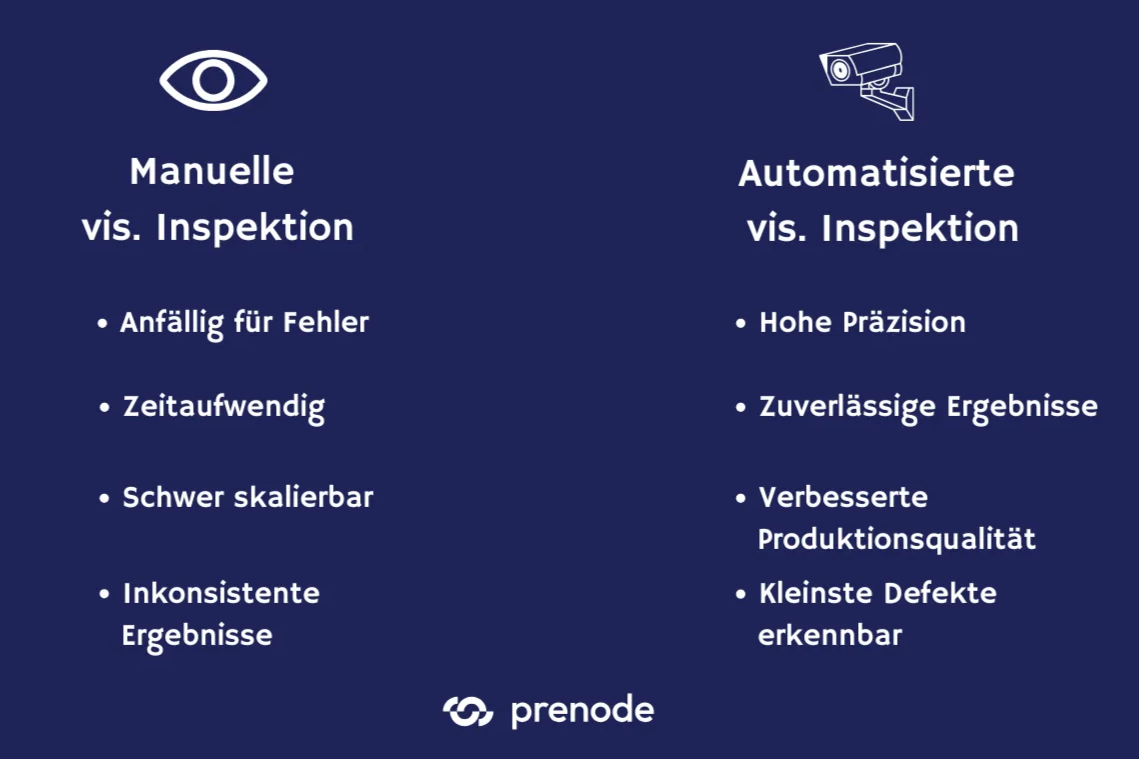
Herausforderungen bei der Einführung
Die Vorteile automatisierter visueller Inspektionen sind klar erkenntlich – doch der Weg zu einer erfolgreichen Implementierung bringt einige Herausforderungen mit sich, die Unternehmen bei der Planung berücksichtigen sollten:
Initialer Integrationsaufwand
Die Einführung eines neuen Inspektionssystems erfordert eine genaue Analyse der bestehenden Prozesse, Maschinen und Umgebungsbedingungen. Die Auswahl geeigneter Kameras, Sensorik, Beleuchtung und Analyseverfahren ist stark abhängig vom spezifischen Anwendungsfall – Standardlösungen sind selten ausreichend. Gerade in bestehenden Produktionslinien kann die Integration zusätzliche mechanische oder steuerungstechnische Anpassungen notwendig mache
Datenmenge und Qualität
Damit KI-Modelle zuverlässig Fehler erkennen, benötigen sie hochwertige Trainingsdaten. In der Praxis ist die Zusammenstellung eines ausreichend großen und ausgewogenen Datensatzes – mit typischen Fehlerbildern – oft eine Herausforderung. Für die Inbetriebnahme müssen diese Daten zunächst erhoben, strukturiert und gegebenenfalls neu klassifiziert werden. Zudem muss sichergestellt werden, dass neue Fehlerarten auch später schnell ins Modelltraining eingebunden werden können.
Validierung vor der Produktivsetzung
Bevor das System in der laufenden Produktion zum Einsatz kommt, sollte eine realistische Machbarkeitsvalidierung erfolgen. Dies geschieht idealerweise in einer separaten Testumgebung oder mit einem Prototypen. Nur so lassen sich unerwartete Abweichungen, technische Grenzen oder betriebliche Einschränkungen frühzeitig erkennen – ohne das Risiko eines direkten Eingriffs in bestehende Prozesse.
Umgang mit Varianz & externen Veränderungen
Produkte können sich in Farbe, Material oder Geometrie unterscheiden. Diese Varianz muss das System zuverlässig erkennen und unterscheiden können – ohne Fehlalarme oder Falschklassifikationen. Gerade bei wechselnden Chargen oder individuellen Varianten erfordert das ein sehr robustes Modelltraining und adaptive Bildverarbeitung. Externe Einflussfaktoren wie Temperatur, Lichtverhältnisse oder Materialchargen müssen dabei möglichst genau definiert und im Modell berücksichtigt werden. Da sich externe Rahmenbedingungen im laufenden Betrieb verändern können – etwa durch neue Materialien, Maschinenupdates oder Umgebungsänderungen – ist es essenziell, das System flexibel und anpassbar zu gestalten.
Akzeptanz im Betrieb
Wie bei jeder Automatisierung kann es zu Vorbehalten im Team kommen – insbesondere, wenn bisher manuell geprüft wurde. Wichtig ist es daher, die Mitarbeitenden frühzeitig einzubinden und aufzuzeigen, dass die Systeme nicht als Ersatz, sondern als Unterstützung zur Qualitätssicherung dienen. Gute Schulungen und transparente Schnittstellen helfen, das Vertrauen in das System aufzubauen.
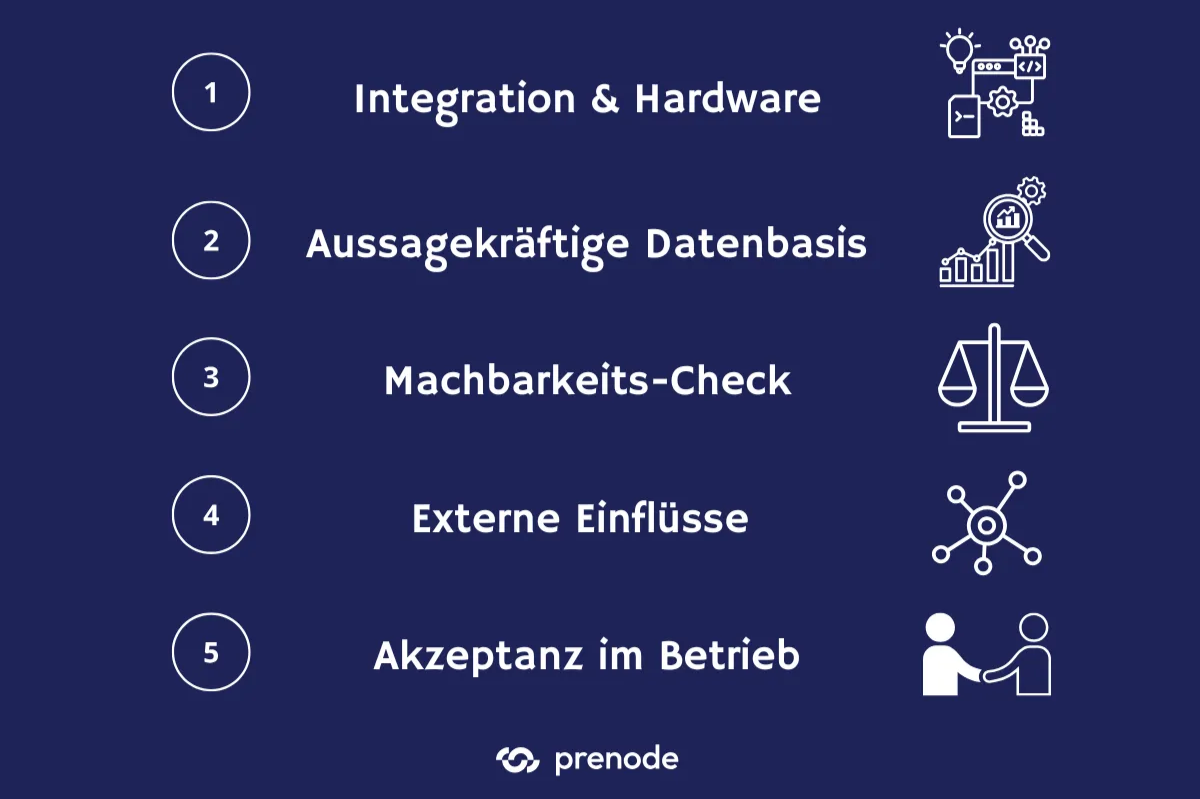
Einführung in den technischen Aufbau einer automatisierten visuellen Inspektion
Die Hardware-Basis bilden meist hochauflösende Industriekameras mit eigenem Processing und Schnittstellen via APIs / SDKs. Diese nehmen Bilder und Tiefendaten in Echtzeit auf – detailgenau und verzerrungsfrei.
Eine optimal abgestimmte Beleuchtung spielt dabei eine zentrale Rolle: Sie sorgt für gleichmäßige Ausleuchtung, reduziert Reflexionen und hebt relevante Merkmale durch gezielte Kontraste hervor.
Die aufgenommenen Daten werden direkt an ein zentrales Rechensystem übermittelt, das die Analyse mithilfe künstlicher Intelligenz durchführt.
Softwareseitig arbeiten moderne Bildverarbeitungstechnologien Hand in Hand mit KI-Modellen. Mithilfe von Machine Learning und Deep Learning werden Defekte nicht nur erkannt, sondern auch automatisch klassifiziert. Gleichzeitig sorgt eine nahtlose Integration in bestehende Systeme – etwa MES- oder ERP-Lösungen – dafür, dass Prüfergebnisse direkt in die Produktionssteuerung einfließen.
Intuitive Benutzeroberflächen ermöglichen es zudem, Fehlerbilder einzusehen, Ursachenanalysen durchzuführen und individuelle Berichte zu generieren – ohne tiefes technisches Vorwissen.
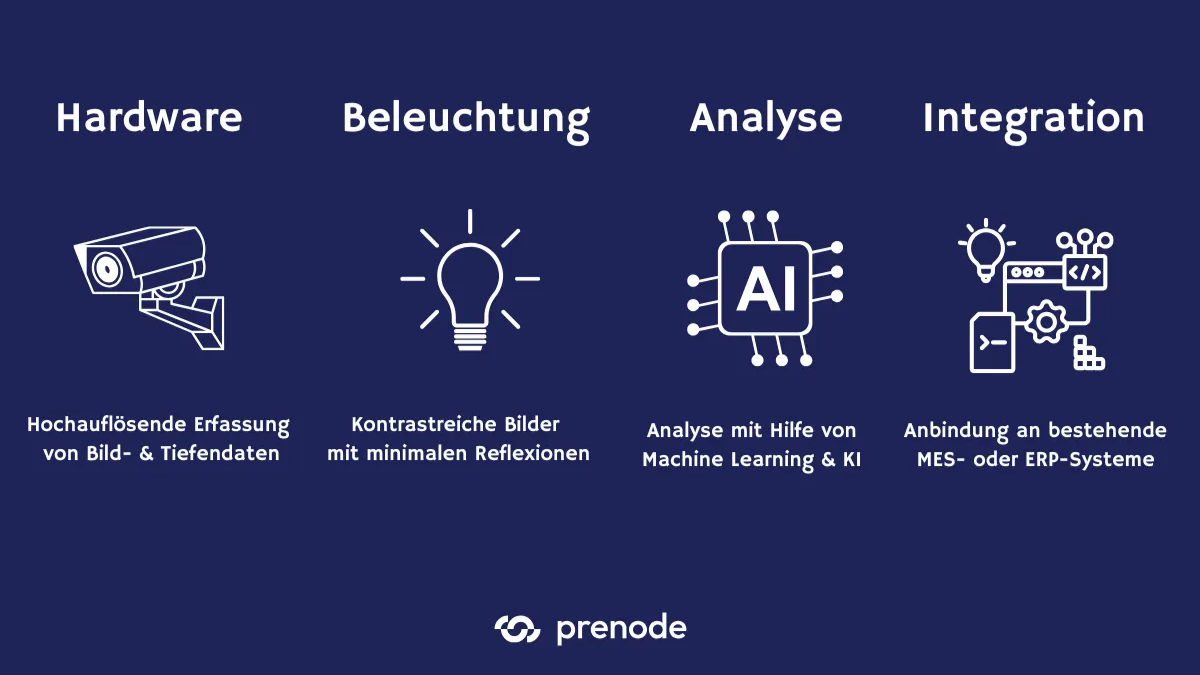
Anwendungsbeispiele für visuelle Inspektion
Ein typisches Anwendungsfeld ist die Erkennung von Oberflächenfehlern wie Kratzern, Dellen oder Rissen – etwa auf Karosserieteilen, Werkzeugen oder Maschinenelementen. Mithilfe hochauflösender Kamerasysteme und intelligenter Bildanalyse lassen sich solche Defekte frühzeitig erkennen, bevor sie in den weiteren Produktionsprozess gelangen. Dadurch wird Ausschuss reduziert und die Qualität konstant hoch gehalten.
Auch bei der Prüfung von Form- und Maßabweichungen – beispielsweise an Stanzteilen oder gelaserten Blechen – sorgt die automatisierte Inspektion für präzise Ergebnisse. Abweichungen von den vorgegebenen Sollmaßen werden in Echtzeit erkannt, sodass schnelle Korrekturen möglich sind und die Maßhaltigkeit der Bauteile gewährleistet bleibt.
Ein weiteres Einsatzgebiet ist die Überwachung von Lötstellen und Schweißnähten. Unregelmäßigkeiten wie unsaubere Lötpunkte oder ungleichmäßige Schweißnähte lassen sich automatisiert identifizieren, wodurch sofortige Anpassungen im Produktionsprozess möglich sind. Das trägt dazu bei, die Prozesssicherheit zu erhöhen und die Produktqualität langfristig zu sichern.
Diese Beispiele zeigen: Automatisierte visuelle Inspektion ist ein vielseitiges Werkzeug für die industrielle Qualitätskontrolle – schnell, zuverlässig und skalierbar. Besonders in Serienfertigungen oder bei sicherheitsrelevanten Komponenten schafft sie die Voraussetzung für gleichbleibend hohe Standards.
AssetCore: Individualisiertes System zur automatisierten visuellen Inspektion
Die Einführung eines Systems zur automatisierten visuellen Inspektion stellt für viele Unternehmen einen strategischen Schritt in Richtung Qualitätssicherung der nächsten Generation dar.
Mit AssetCore von prenode steht eine leistungsfähige Lösung zur Verfügung, die nicht nur technische Präzision bietet, sondern auch gezielt auf die individuellen Anforderungen der Produktion abgestimmt werden kann.
Unsere Herangehensweise ist systematisch und praxisnah – mit dem Ziel, ein robustes, skalierbares und zukunftssicheres Inspektionssystem zu implementieren. Im ersten Schritt erfassen wir gemeinsam mit dem Kunden die spezifischen Anforderungen vor Ort. Dabei werden die Gegebenheiten der Fertigungsumgebung analysiert, relevante Prüfparameter definiert und die passenden Komponenten – wie Kameras, Sensorik, Beleuchtung und Edge-Devices – ausgewählt.
Auf dieser Basis entwickeln wir ein maßgeschneidertes System, das in die bestehende Produktionsumgebung integriert wird. Dabei kommt KI-gestützte Fehlererkennung zum Einsatz, die auf realen Produktionsdaten trainiert und feinjustiert wird. Durch gezieltes Machine Learning wird sichergestellt, dass das System nicht nur zuverlässig Fehler erkennt, sondern auch mit hoher Genauigkeit misst. Bestehende Schnittstellen zu Maschinensteuerungen oder Qualitätssicherungssystemen werden dabei nahtlos angebunden.
Nach erfolgreicher Inbetriebnahme bietet AssetCore eine Vielzahl von Funktionen, die den Betrieb effizient und transparent gestalten. Fehler werden in Echtzeit erkannt und analysiert, automatisch dokumentiert und in strukturierte Prüfberichte überführt. Diese Berichte fließen direkt in das Qualitätssystem ein und schaffen die Grundlage für fundierte Entscheidungen und kontinuierliche Prozessverbesserung.
Über Remote-Zugriff kann das System bequem gewartet und aktualisiert werden – ein großer Vorteil, insbesondere in dezentralen Fertigungsstrukturen. Zudem ermöglicht die Architektur von AssetCore auch ein einfaches Retrofit ähnlicher Maschinen im Bestand, was die Skalierung innerhalb des Werks erheblich vereinfacht.
All das macht AssetCore zu einem verlässlichen Partner für moderne Industrieunternehmen, die Qualität systematisch gewährleisten wollen.
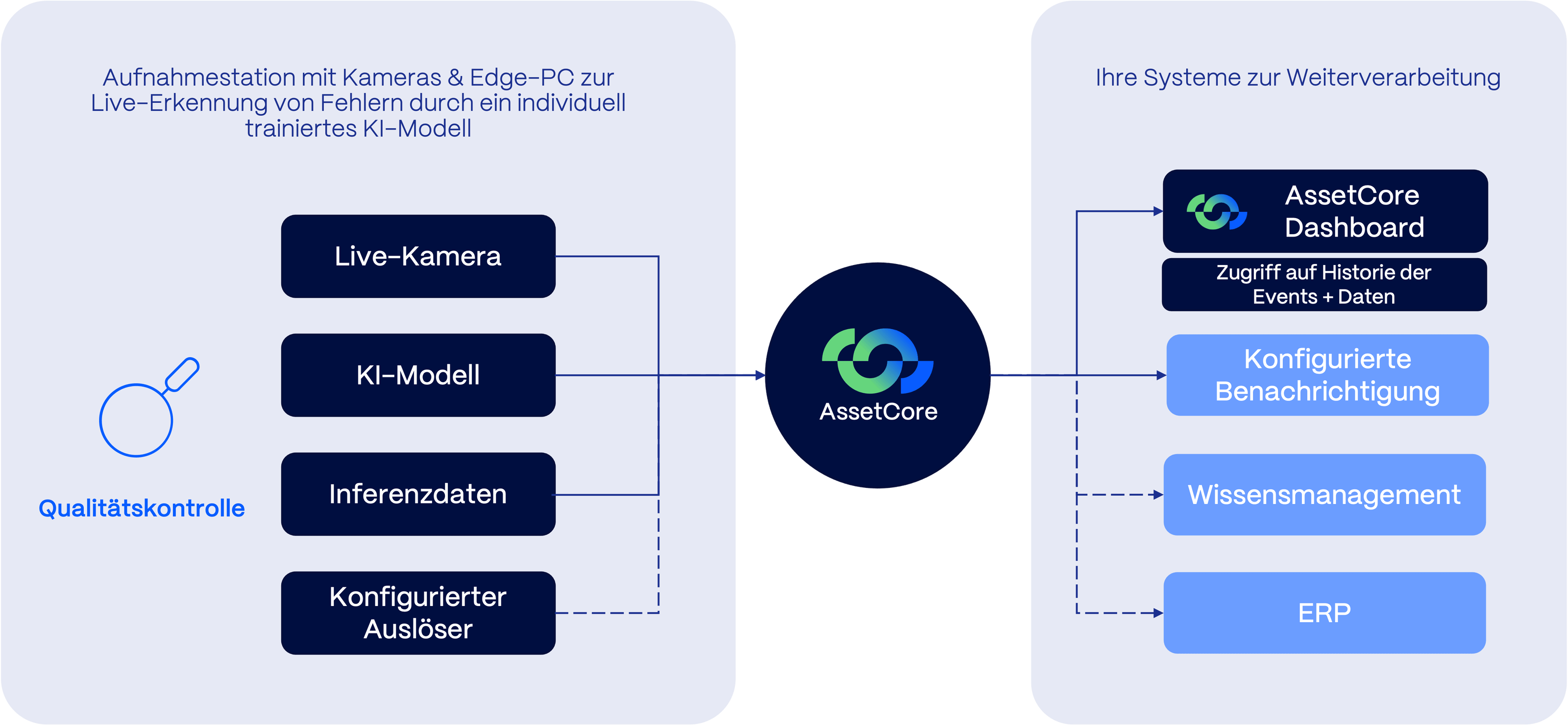
Teilen Sie diesen Artikel