Automated visual inspection
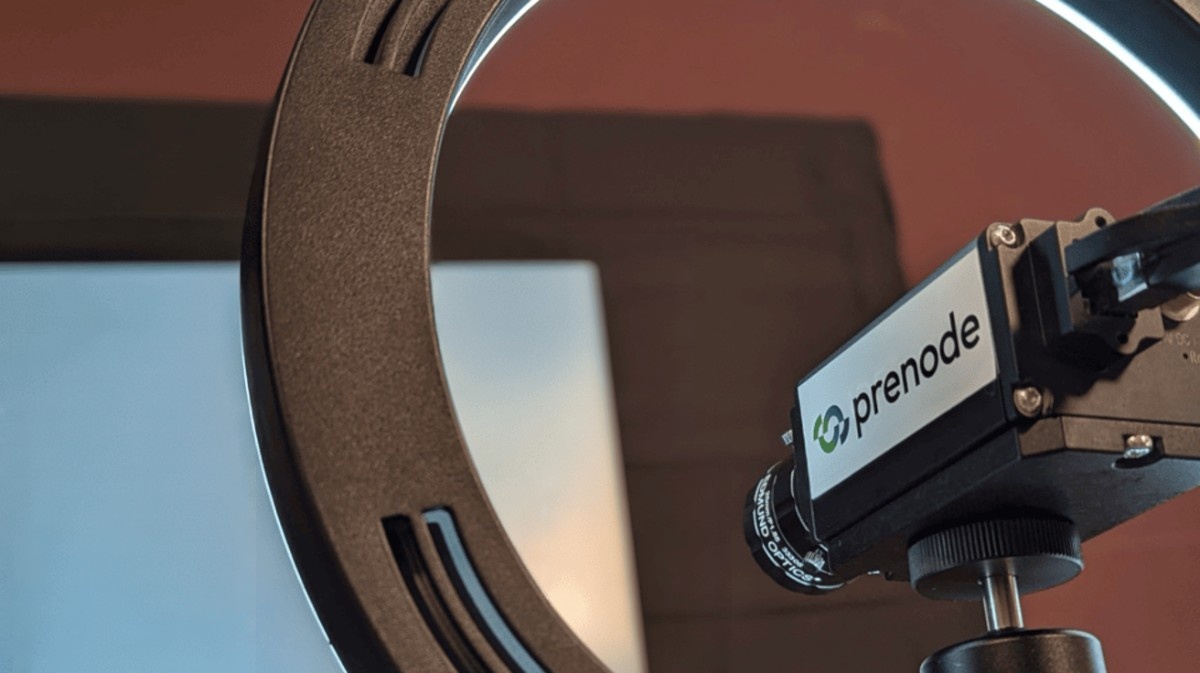
Visual inspection is an essential part of quality assurance in industrial production. It is used to identify faulty products before they reach the end customer. While manual visual inspection was the standard for decades, modern technologies based on artificial intelligence and image processing are bringing significant improvements. In this article, we look at the challenges of manual inspection, the benefits of automated testing, and the technical design of such systems.
Manual visual inspection issues
Manual visual inspection is still widely used in many manufacturing companies, but poses a variety of challenges. One of the biggest drawbacks lies in the inconsistent assessment of errors. Human control is, of course, subjective — factors such as daily status, concentration, or experience of the reviewer influence the quality of the assessment. As a result, errors are identified differently or even overlooked.
In addition, manual testing processes are usually only carried out on a random basis. This limited depth of testing entails the risk that defective parts remain undetected and are further processed or delivered. At the same time, visual checks are time-consuming. Long testing times slow down the production process, create bottlenecks and reduce efficiency — particularly with increasing quantities or a wide range of products.
Manual inspection is also economically problematic. The costs for qualified audit personnel are high, and additional expenses arise from scrap, rework and inefficient processes. All of this has a negative impact on profitability. If quality defects are not identified in time, this can also lead to complaints and dissatisfied customers. Trust in the brand suffers — and so does long-term customer loyalty.
Another problem lies in the lack of standardization. Since testing processes depend heavily on individual people, the results are difficult to compare and barely reproducible. This makes both quality control and continuous process optimization difficult.
Overall, it shows that manual visual inspection is vulnerable, cost-intensive and is increasingly a limiting factor for manufacturing companies.
Benefits of automated visual inspection
Modern, AI-based inspection systems detect even the smallest defects that escape the human eye. They work with a high level of consistency and deliver reproducible results, regardless of external influences such as fatigue or subjective assessments.
Automated visual inspection can be integrated directly into the production line. As a result, all parts produced are tested, not just random samples. This minimizes the risk of delivering faulty products and enables an immediate response to quality issues.
The reduction of waste and improvements saves companies considerable costs. In addition, inspection systems provide valuable analytical data that can be used to further optimize production processes. In the long term, this leads to improved efficiency and product quality.
AI-based inspection systems can be quickly trained for new product variants, which enables flexible adaptation to different requirements. In addition, these systems can be easily extended to multiple production lines or locations.
All inspection data collected can be saved and analyzed. This makes it possible to identify long-term quality problems and take targeted measures to prevent errors. Companies thus gain valuable insights into their production processes and can continuously improve them.
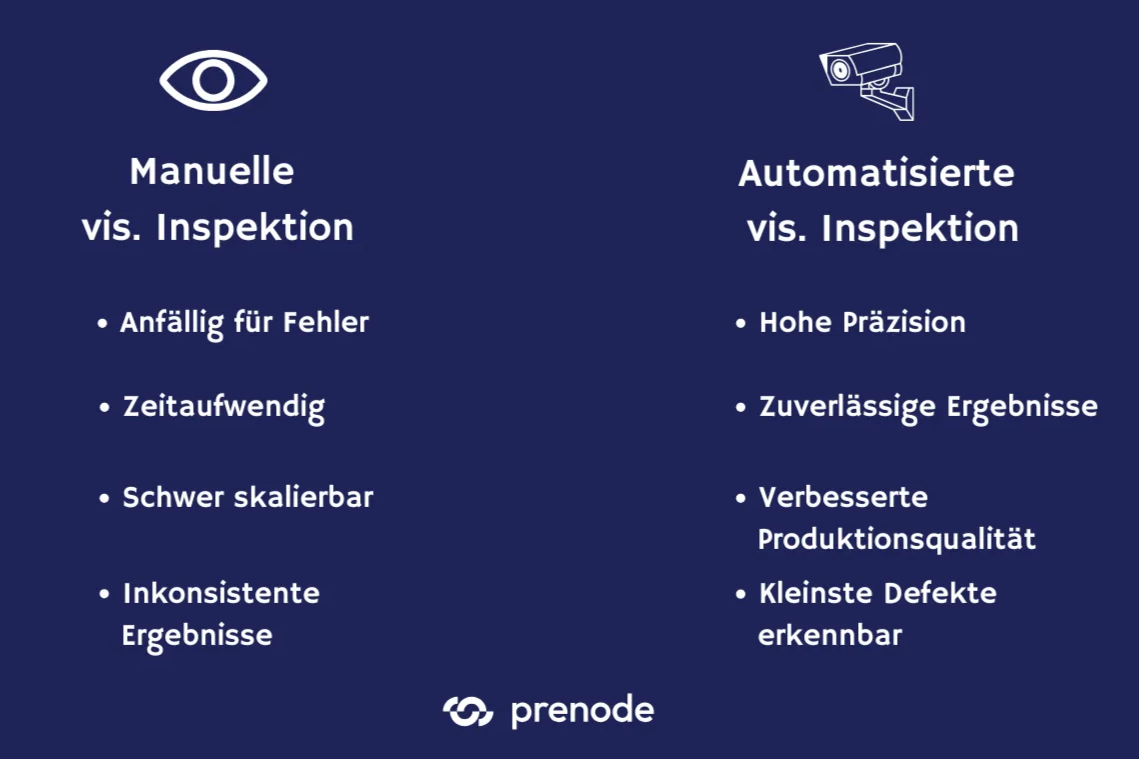
Implementation challenges
The benefits of automated visual inspections are obvious — but the road to successful implementation involves some challenges that companies should consider when planning:
Initial integration effort
The introduction of a new inspection system requires a detailed analysis of existing processes, machines and environmental conditions. The selection of suitable cameras, sensors, lighting and analysis methods depends heavily on the specific application — standard solutions are rarely sufficient. Especially in existing production lines, integration may require additional mechanical or control adjustments
Data volume and quality
In order for AI models to reliably identify errors, they need high-quality training data. In practice, compiling a sufficiently large and balanced data set — with typical error patterns — is often a challenge. For commissioning, this data must first be collected, structured and, if necessary, reclassified. In addition, it must be ensured that new types of errors can also be quickly integrated into model training later on.
Validation before going live
Before the system is used in ongoing production, a realistic feasibility validation should be carried out. Ideally, this is done in a separate test environment or with a prototype. This is the only way to identify unexpected deviations, technical limits or operational restrictions at an early stage — without the risk of direct intervention in existing processes.
Dealing with variance & external changes
Products may differ in color, material, or geometry. The system must be able to reliably recognize and differentiate this variance — without false alarms or false classifications. Especially with changing batches or individual variants, this requires very robust model training and adaptive image processing. External influencing factors such as temperature, lighting conditions or material batches must be defined as precisely as possible and taken into account in the model. Since external conditions can change during operation — for example due to new materials, machine updates or environmental changes — it is essential to make the system flexible and adaptable.
Acceptance in the company
As with any automation, there can be reservations within the team — especially if manual testing has been carried out so far. It is therefore important to involve employees at an early stage and to show that the systems do not serve as a substitute but as support for quality assurance. Good training and transparent interfaces help build trust in the system.
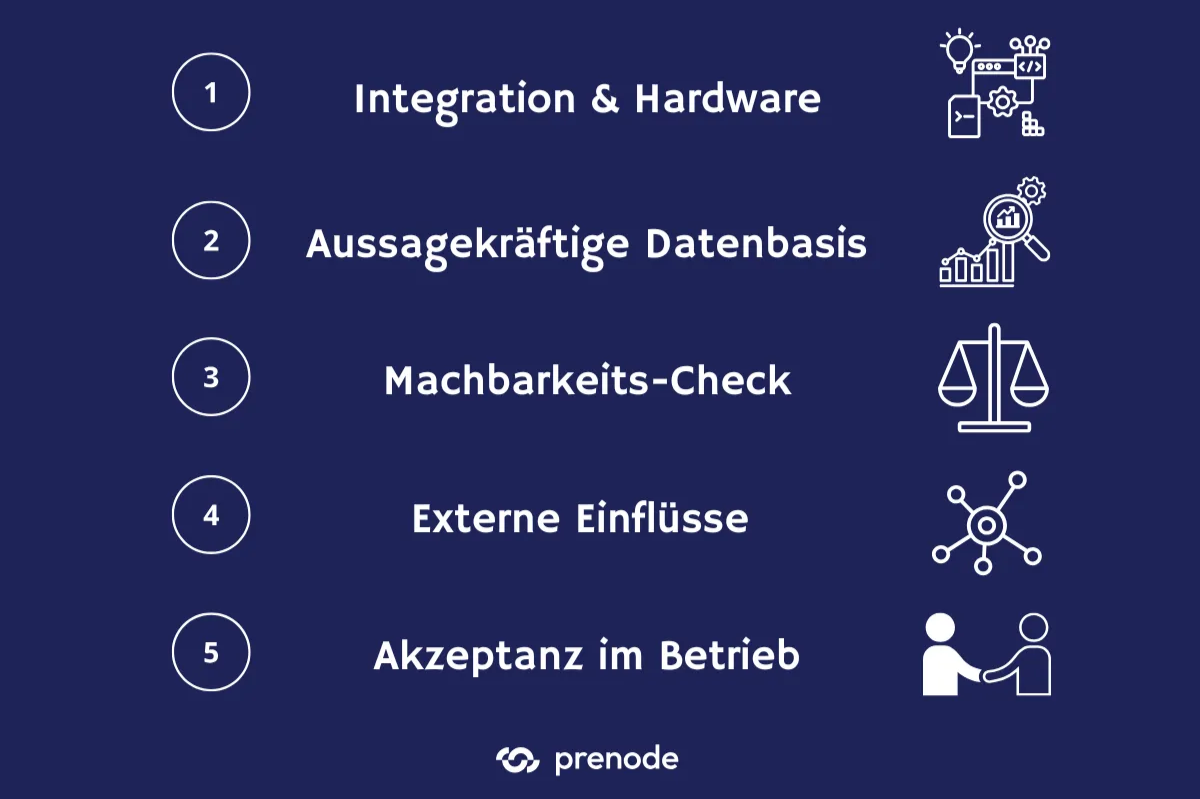
Introduction to the technical structure of an automated visual inspection
The hardware basis is usually high-resolution industrial cameras with their own processing and interfaces via APIs/SDKs. They capture images and depth data in real time — precisely and without distortion.
Optimally coordinated lighting plays a central role here: It ensures uniform illumination, reduces reflections and highlights relevant features through targeted contrasts.
The recorded data is transmitted directly to a central computing system, which carries out the analysis using artificial intelligence.
On the software side, modern image processing technologies work hand in hand with AI models. With the help of machine learning and deep learning, defects are not only identified but also automatically classified. At the same time, seamless integration into existing systems — such as MES or ERP solutions — ensures that test results flow directly into production control.
Intuitive user interfaces also make it possible to view error patterns, carry out root cause analyses and generate individual reports — without deep technical knowledge.
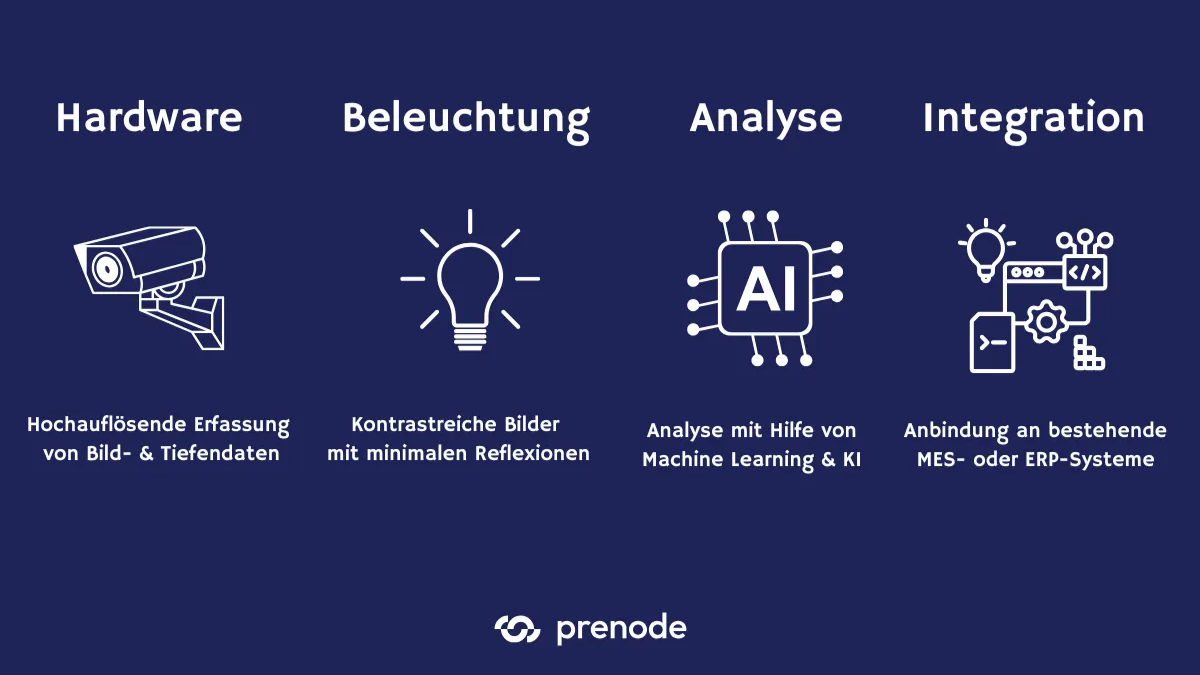
Visual inspection application examples
A typical field of application is the detection of surface defects such as scratches, dents or cracks — for example on car body parts, tools or machine elements. With the help of high-resolution camera systems and intelligent image analysis, such defects can be identified at an early stage before they enter the further production process. As a result, waste is reduced and quality is kept consistently high.
Automated inspection also ensures precise results when checking shape and dimensional deviations — for example on punched parts or lasered sheets. Deviations from the specified target dimensions are detected in real time, so that rapid corrections are possible and the dimensional accuracy of the components is guaranteed.
Another area of application is the monitoring of solder joints and welds. Irregularities such as dirty solder points or uneven welds can be identified automatically, which allows immediate adjustments to the production process. This helps to increase process reliability and ensure product quality in the long term.
These examples show that automated visual inspection is a versatile tool for industrial quality control — fast, reliable and scalable. Especially in series production or safety-relevant components, it creates the conditions for consistently high standards.
AssetCore: Individualized system for automated visual inspection
For many companies, the introduction of an automated visual inspection system represents a strategic step towards next-generation quality assurance.
With AssetCore prenode offers a powerful solution that not only offers technical precision, but can also be specifically tailored to individual production requirements.
Our approach is systematic and practical — with the aim of implementing a robust, scalable and future-proof inspection system. As a first step, we work with the customer to identify the specific requirements on site. The conditions of the manufacturing environment are analyzed, relevant test parameters are defined and the appropriate components — such as cameras, sensors, lighting and edge devices — are selected.
On this basis, we develop a tailor-made system that is integrated into the existing production environment. This uses AI-based fault detection, which is trained and fine-tuned on real production data. Targeted machine learning ensures that the system not only reliably detects errors, but also measures them with a high level of accuracy. Existing interfaces to machine control systems or quality assurance systems are seamlessly connected.
After successful start-up, AssetCore offers a variety of functions that make operations efficient and transparent. Errors are identified and analyzed in real time, automatically documented and converted into structured test reports. These reports flow directly into the quality system and create the basis for well-founded decisions and continuous process improvement.
Remote access makes it easy to maintain and update the system — a major advantage, particularly in decentralized manufacturing structures. In addition, AssetCore's architecture also makes it easy to retrofit similar machines in inventory, which significantly simplifies scaling within the plant.
All of this makes AssetCore a reliable partner for modern industrial companies that want to systematically guarantee quality.
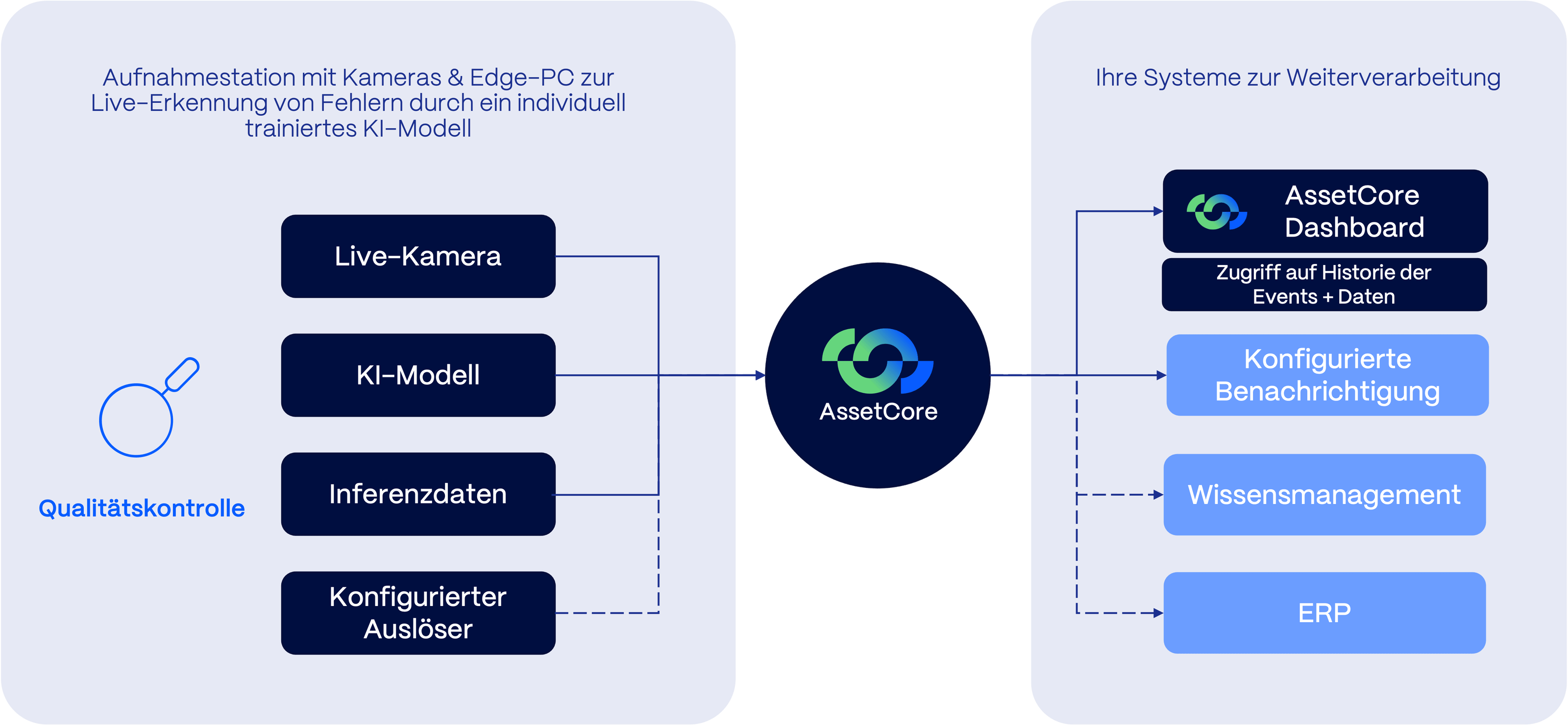
Share this article