Smart Connectivity: How OPC UA and Azure pave the way for successful IoT projects
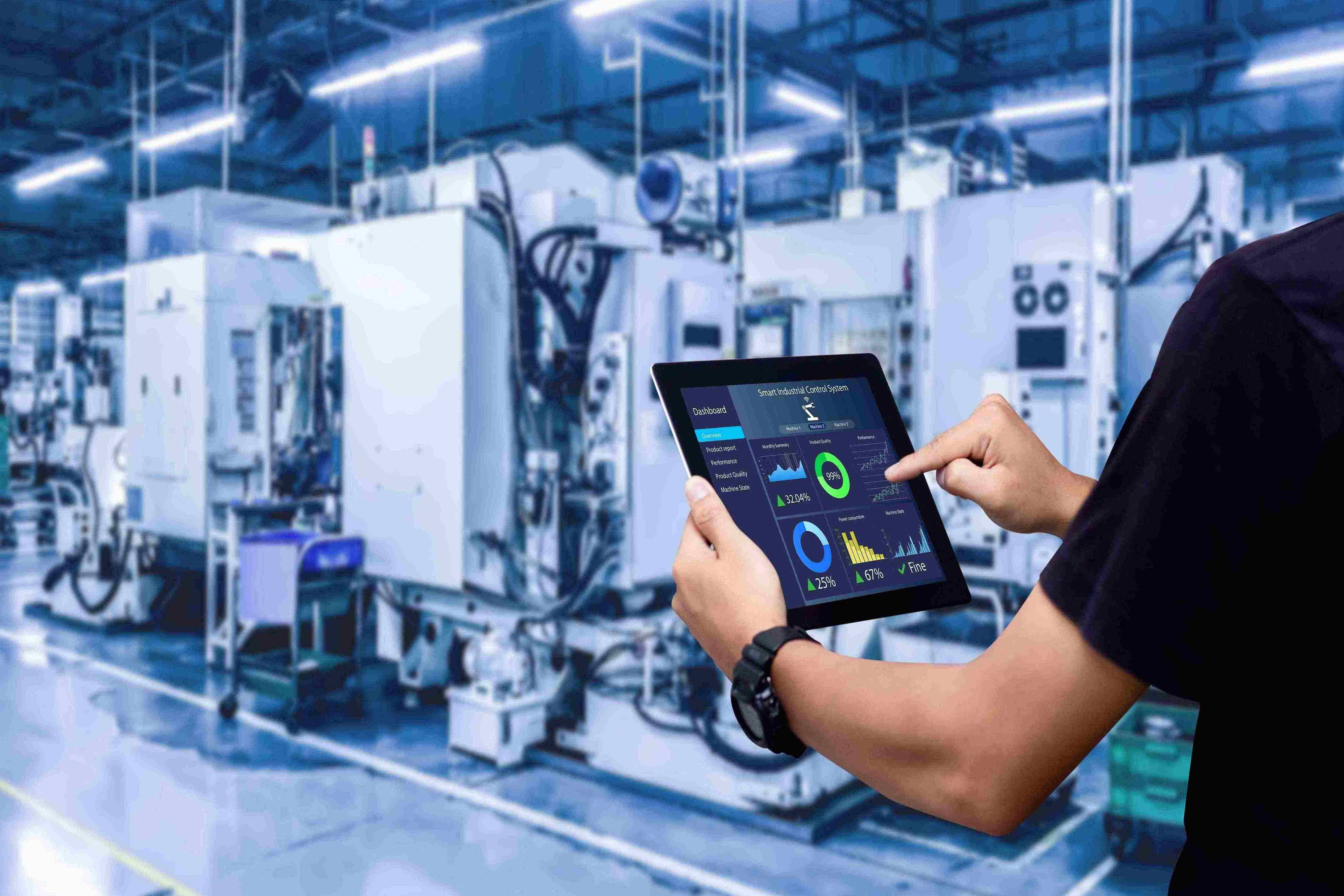
To start and successfully run an IoT project, you need to be able to easily access and process information from many different devices, sensors, and machines in your IoT network. To do this, it is important that all these components can exchange data with each other in the same way: The OPC UA protocol provides the bridge to make this possible.
The cross-linking of different devices offers many new possibilities to improve your operation. Imagine, for example, monitoring the operating temperature and energy consumption at a machine in your production via external sensors and automatically receiving a notification when critical values are exceeded.
This enables you to identify and prevent potential problems at an early stage. This ability to obtain data and communicate forms the basic framework for effective IoT solutions and enables new potential for the digital factory.
The OPC UA Standard
OPC UA (Open Platform Communications Unified Architecture) is the heart of industrial automation and to allows different machines and devices to communicate with each other, regardless of their origin or technological basis. It uses a "client-server" model: A client requests data from the server and the server provides it in a structured format.
Data is transferred using common protocols such as TCP/IP and can take place both within local networks and over the Internet. OPC UA places particular emphasis on security aspects and encryption, e.g., through certificate-based authentication, where each device and user use its own digital certificate for access control.
OPC UA also forms the basis for more advanced technologies such as umati (Universal Machine Tool Interface). The umati initiative aims to improve the networking and interoperability of machine tools from different manufacturers.
While OPC UA builds the bridge for data exchange, umati provides a common language for machines to exchange and comprehend data. This opens the potential for a networked factory environment in which machines can cooperate seamlessly - an exciting prospect that is already taking shape today thanks to OPC UA.
From the Machine to the Cloud – With OPC UA and Azure IoT
To take advantage of OPC UA in practice, prenode uses the Azure IoT solution. This has three key advantages:
- The OPC UA standard is widely used and allows seamless integration of different machines and devices. This greatly accelerates the implementation of innovative IoT solutions.
- The security features of OPC UA in combination with the protection mechanisms of the Azure IoT solution provide a secure environment for data transmission and access control, thus laying the foundation for trusted IoT applications.
- Microsoft Azure Cloud is a leader in IIoT device networking and “Industrie 4.0” deployment, providing secure software components for diverse use cases. Using these components allows rapid scaling and prevents vendors lock-in for our customers.
The diagram below illustrates the typical process for monitoring key production metrics using OPC UA and individual Azure components.
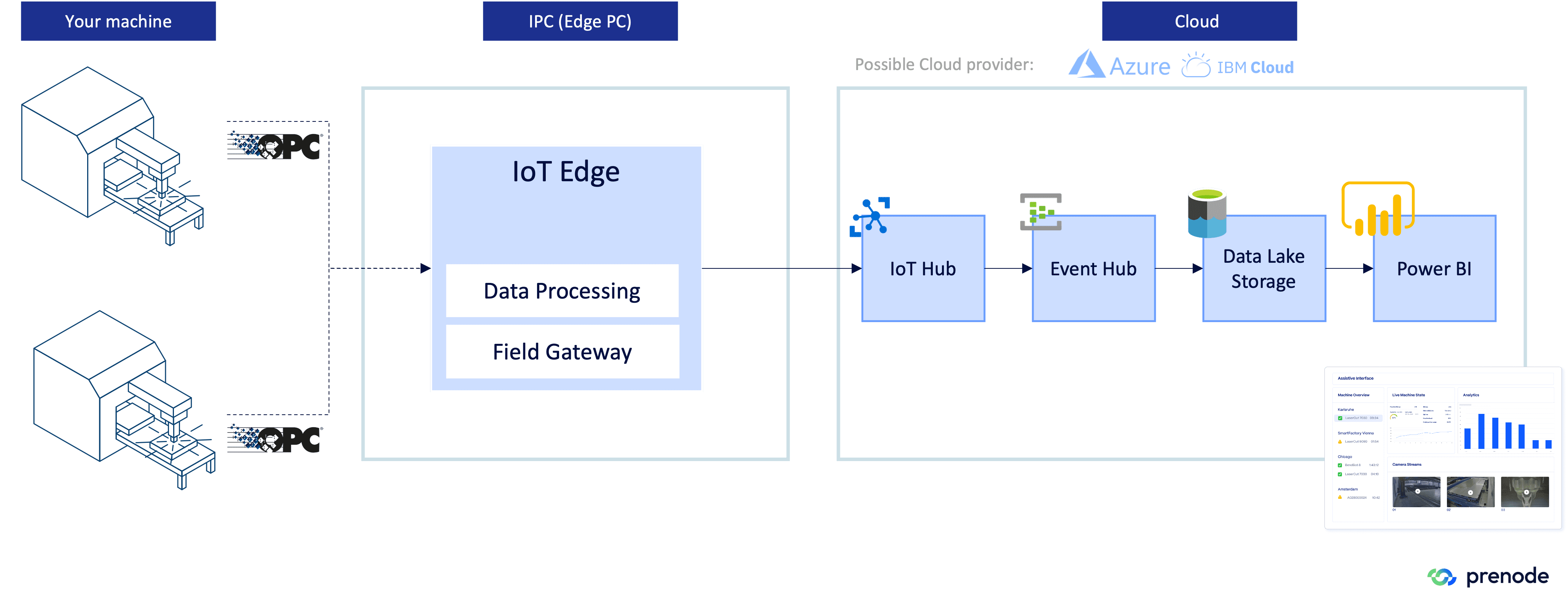
The Azure IoT Hub is offered by Microsoft as a managed cloud service platform to seamlessly integrate IoT devices into Azure. This securely connects IoT devices to the Azure cloud, collecting and effectively analyzing data.
This makes it possible to react to short-term changes and create new, intelligent IoT applications. The following components are typically used:
- IoT Edge Komponente - The OPC UA signals are received locally by the IoT Edge component, processed, and forwarded to the IoTHub.
- IoTHub - The IoTHub enables a secure, bidirectional connection between edge and cloud.
- EventHub - Various applications (including Power BI) can access the data via the Event Hub.
- Power BI - In Power BI, the desired KPIs are displayed in visual reports (further processing via e.g., Excel possible)
Typical applications
The combination of Azure IoT and OPC UA opens a wide range of benefits and opportunities to intelligently process production data and derive insights from it. Some of the most important use cases for industry today are:
- Digital Twin: The integration of Azure IoT and OPC UA enables the creation of digital twins. These virtual representations of real physical assets or products offer a range of possibilities. By continuously collecting and transferring data to the cloud, the condition of the real object can be monitored and analyzed in real time. This enables better prediction of maintenance needs, more accurate simulation of processes, and improved efficiency in product development and optimization.
- Smart Manufacturing: Connecting machines to the cloud enables the implementation of smart manufacturing concepts. Integrating IoT data into production lines improves flexibility, enables more precise production planning, and boosts automation, resulting in increased production output and improved quality control.
- Predictive Maintenance: By continuously collecting and transferring machine data to the cloud, companies can develop preventive maintenance strategies. Analyzing this data enables the identification of maintenance needs before failures occur, which increases uptime and reduces unplanned downtime.
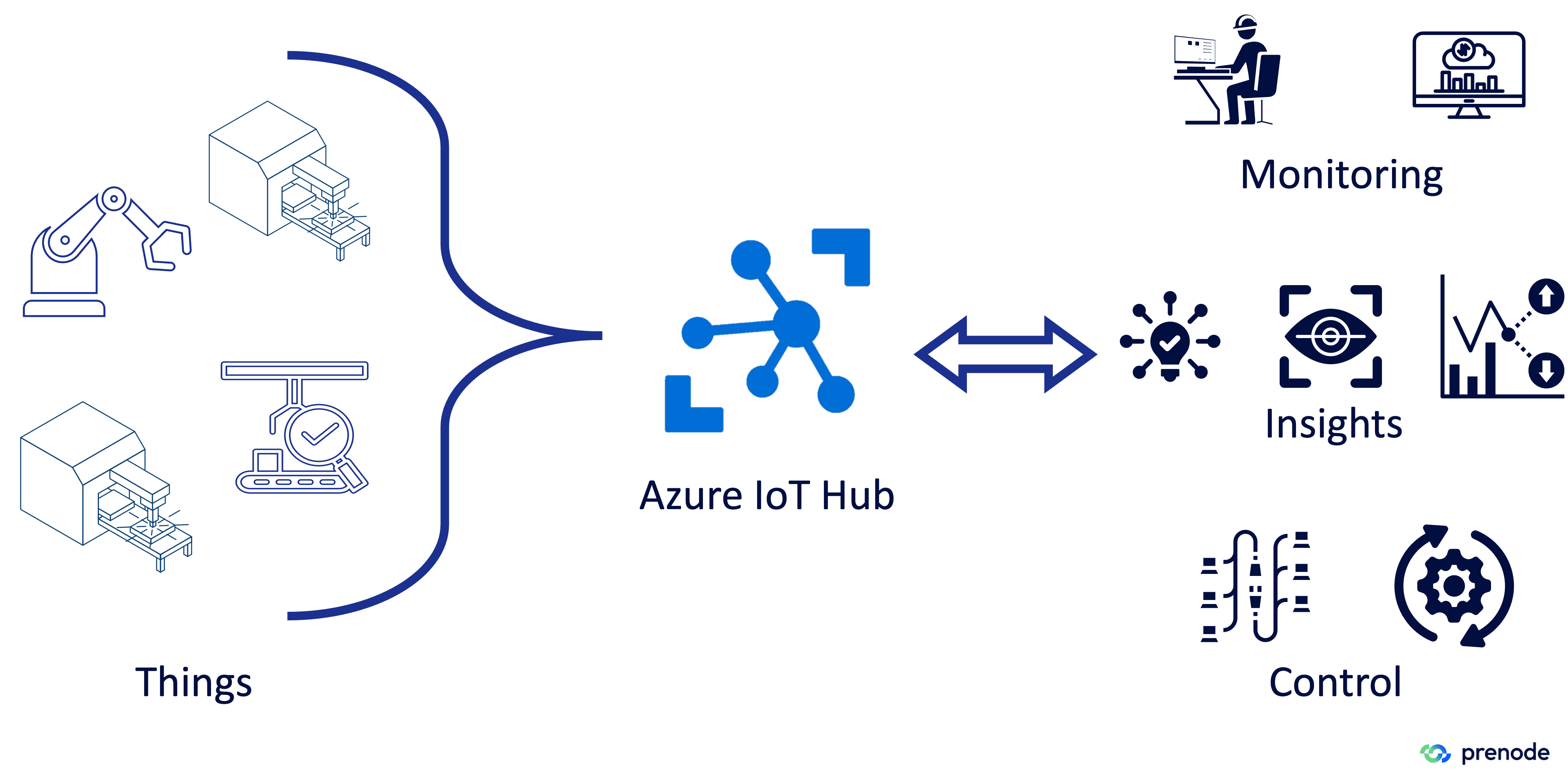
OPC UA & Azure IoT in production
As a result, the combination of Azure IoT and OPC UA opens up new opportunities for enterprises to rely on comprehensive data analytics and intelligent decision-making to optimize operations, increase productivity, and reduce costs. The successful application of these technologies plays a critical role in the transformation of traditional businesses into connected, digital and future-proof enterprises.
At prenode, together with our customer TRUMPF, we were able to implement an innovative and Microsoft award-winning technology that enables the Equipment-as-a-Service (EaaS) model in the sheet metal industry, using Azure components and OPC UA. TRUMPF experts in the Remote-Control Center are able to control the highly productive machines with the optimal settings and solve production problems directly from a distance.
Learn more in our success story: Driving TRUMPF's Equipment-as-a-Service (EaaS) business model with prenode remote operations solution
Share this article